Have you ever heard of the “Coffee 2050 Problem” that has been the subject of much concern in recent years?
The “Coffee 2050 Problem,” announced by World Coffee Research (WCR), an international research organization, is that the number of areas suitable for growing Arabica, which accounts for approximately 60% of the world's coffee bean production, will be reduced by half by 2050. It is said that climate change due to global warming is the main reason for this, with rising temperatures and humidity, epidemics of “rust disease,” and droughts making land that was previously suitable for coffee cultivation unsuitable.
ORIGAMI products are manufactured in Toki City, located in the Tono region of Gifu Prefecture, where Mino ware has grown and expanded.
Similar to the coffee bean depletion problem, the mines that are the assets of this Mino ware are also in a depletion situation.
SDG'S are now standard today, but ORIGAMI, as a “manufacturer” of coffee equipment, will embody a way of dealing with them that is only possible because of who we are.
―― As an original brand with a background in Mino ware culture, we constantly create appealing products while reducing waste and reusing valuable resources. ――
What should be the ideal brand that can freely create what we want to create?
To think about what is truly necessary in today's world, not to create waste, and to create new products and spread their value toward that end.
We believe that activities to explore the correct use of limited resources and to connect them to the future are the kind of manufacturing that will be needed in the world in the future.
―― with a view to eventually revising inspection standards so drastic that “disposal” is no longer an option. ――
In order to protect the limited resources surrounding manufacturing in the ceramics industry, we also believe it is necessary to review the criteria for minor defects in our products.
Small flaws found during inspection during the manufacturing process or in warehouses or stores, or slightly blurred printing of logos, etc.
Since they are still forced to dispose of them, one way to improve the situation is not to choose to dispose of them, but to inspect and sell them under new standards that will also reduce their environmental impact.
While striving to improve product management, including the manufacturing process and subsequent storage environment, we will shift to sales where customers are convinced to purchase our products and agree with the concept of this initiative itself.
ORIGAMI's factory is located in a land environment favorable for the production of porcelain products, and plans, manufactures, and sells approximately 10,000 different types of products annually
.
While we are proud of the number of products we produce, there are many products that we have no choice but to discard due to the strict inspection standards of the entire ceramics industry, such as bubbles and fine iron powders created during firing, which are treated as defective products.
One of the main reasons why the ceramic industry originally developed as Mino ware was because of the “resources” provided by nature.
In this land, “raw material soil” from which various types of clay can be produced, “neutral soft water” suitable for ceramic production, and “red pine trees” that are the source of the high fire power necessary for firing could be collected.
The environment in which all of these are available is a unique feature of the Mino region.
In addition, because of the variety of clays used for pottery in various regions of Japan, such as gairo-me clay, kibushi clay, sokei, saba, and silica sand, Tono has continued to produce and use a blend of various materials instead of using a single material as in other regions.
The soil used for “ReWork” products is made from a mixture of more than 20% of the company's own waste products that have been finely crushed and mixed into the soil, taking advantage of the concept of Mino ware, where it was common practice to use blended soil rather than a single raw material. We will practice an “in-house completion cycle” in which waste products that are unavoidably generated are re-created and sold as our own products again.
Since we do not have to collect waste from other companies or gather waste from each household, we do not have to spend the labor and costs associated with collecting waste.
However, in the production of clay, which is made by mixing fine crushed waste products and crushed powder with soil, “re-production and commercialization” can be realized only through the network of Mino ware production areas.
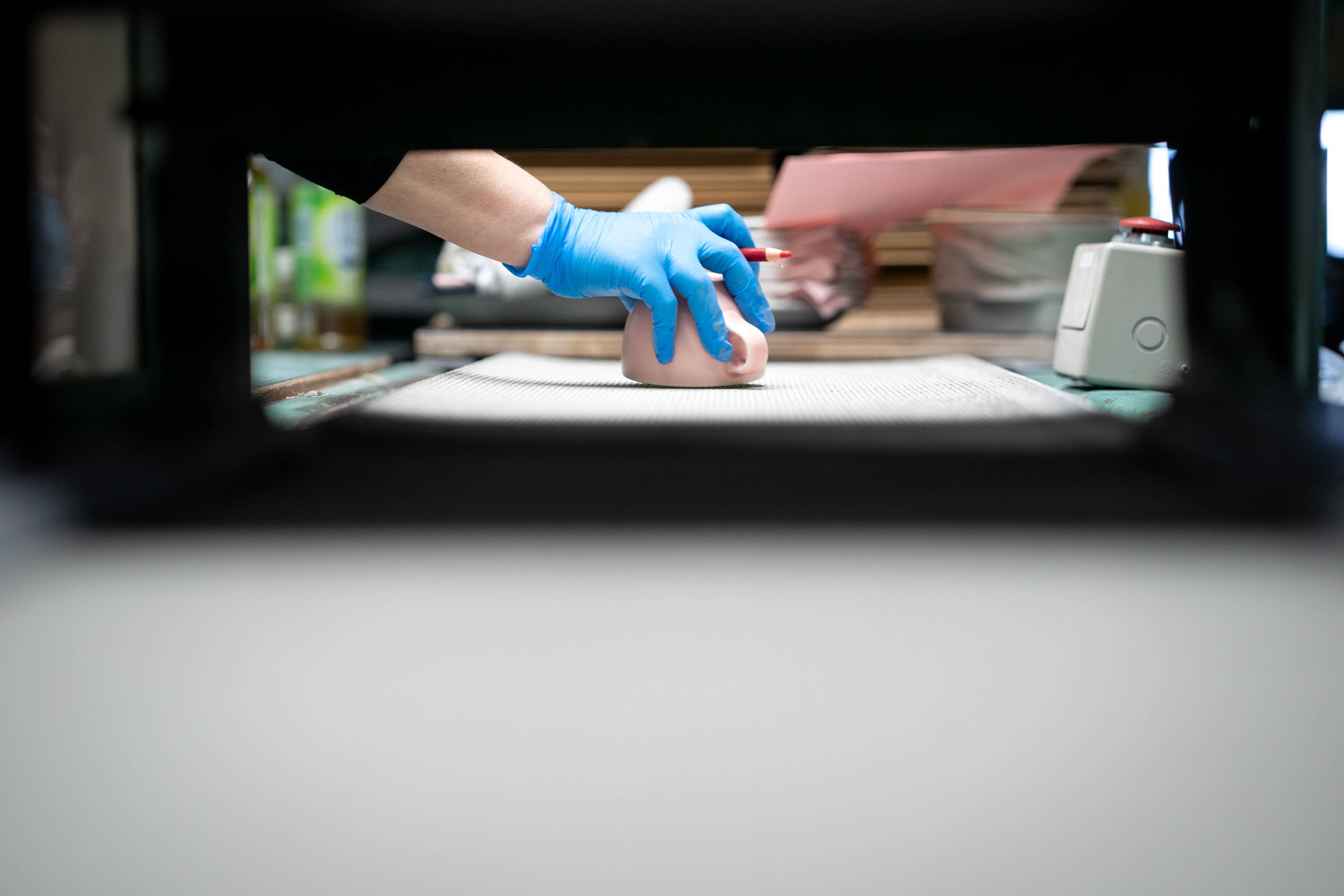
Inspection zone in our factory.
All products after manufacturing is completed are carefully inspected one by one by human eyes.
Only products that have passed strict quality standards and passed checkpoints such as pinholes, iron powder, cracks, and uneven color/browning will be sold as good products.
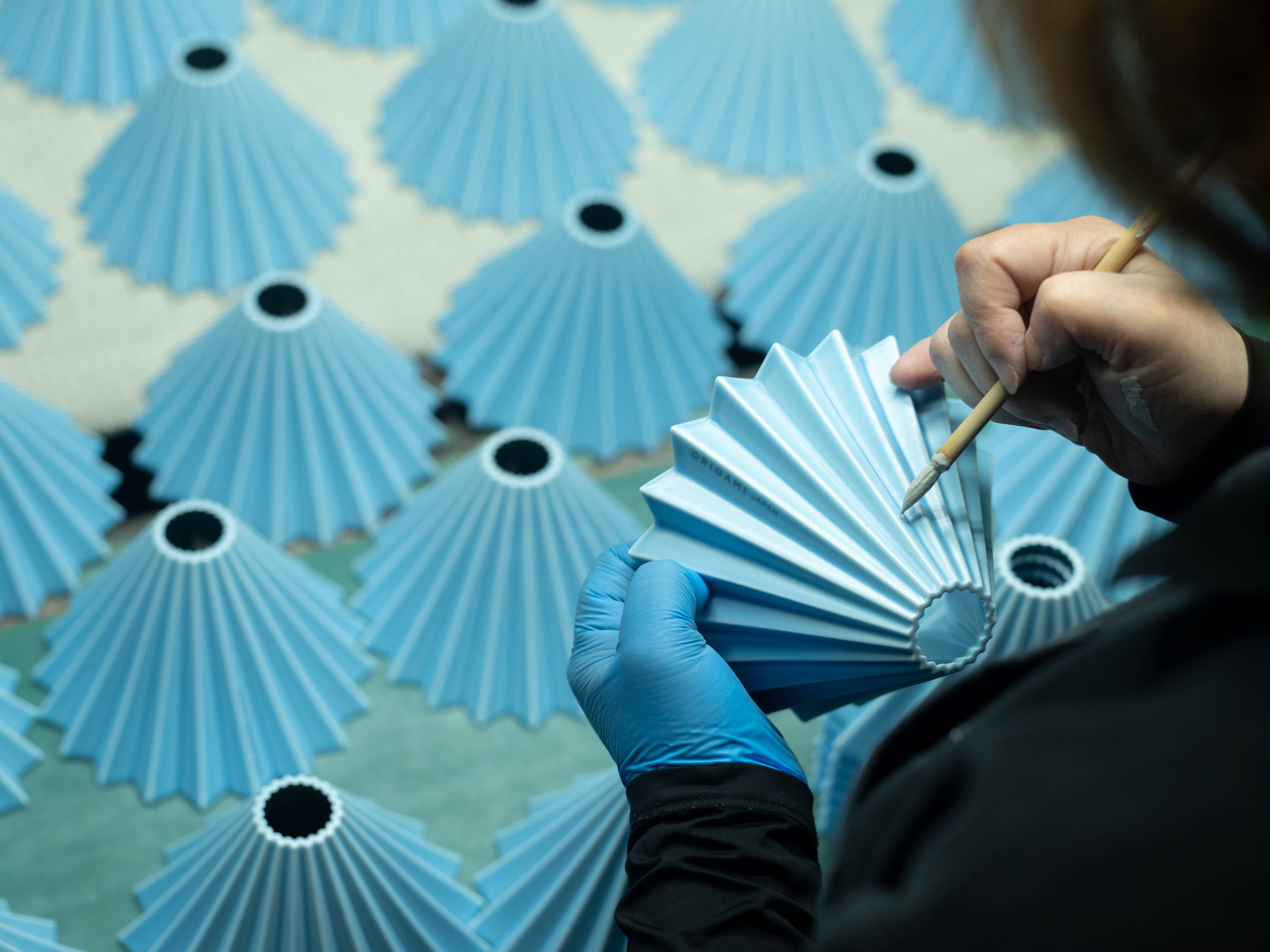
Discarded items used in the ReWork collection are those that have leaked from this strict quality standard, but may be sold as good quality items if they are cared for by our craftsmen during inspection.
As one of the first steps, we carefully inspect the waste products to ensure that they are not treated as waste.
Only those products that still fail to meet our quality standards are consolidated and stored in-house, and once a certain amount has been collected
, they are moved to the pulverization process.
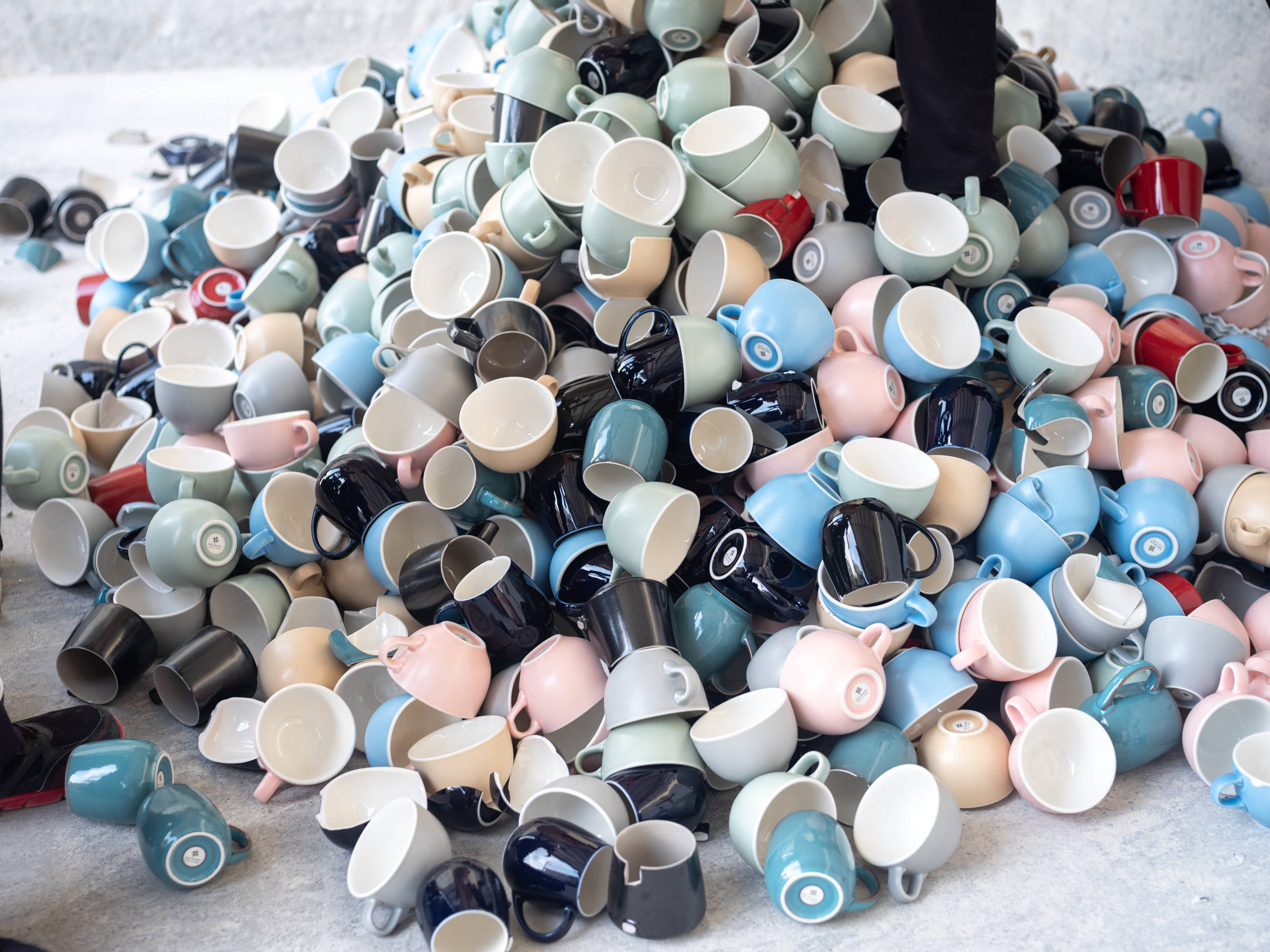
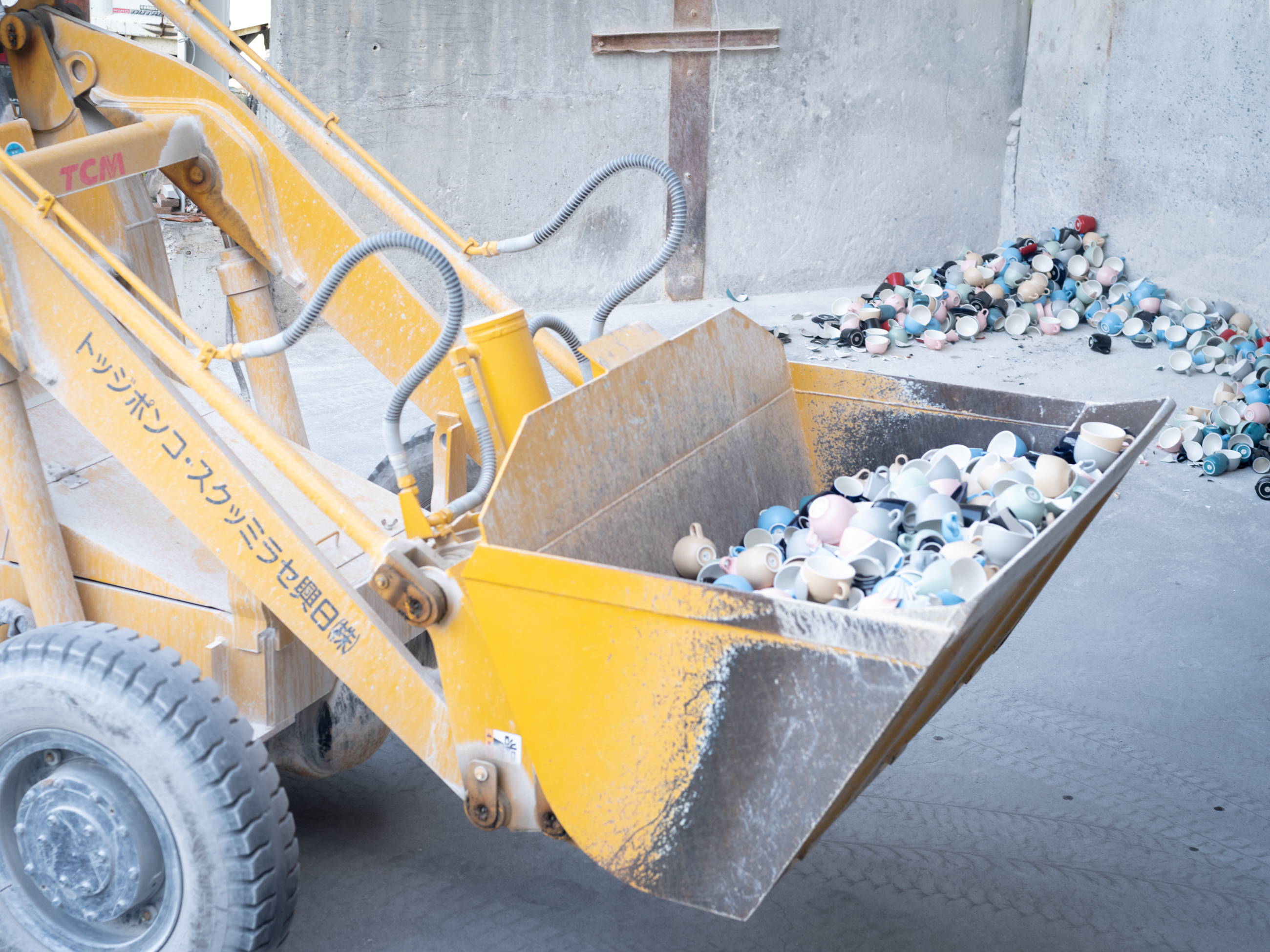
Process 3: Defective products are dismantled, crushed, and ground into powder.
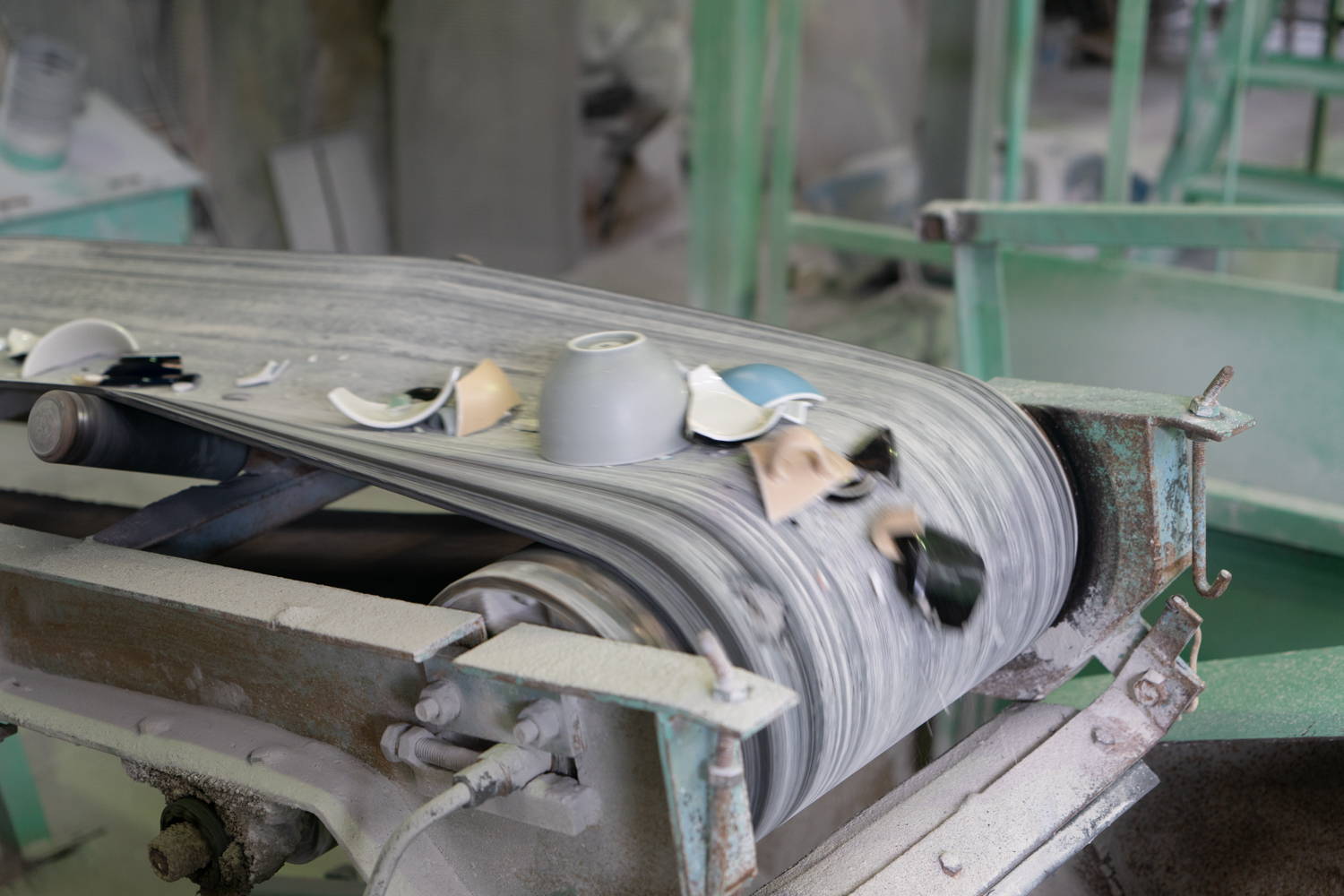
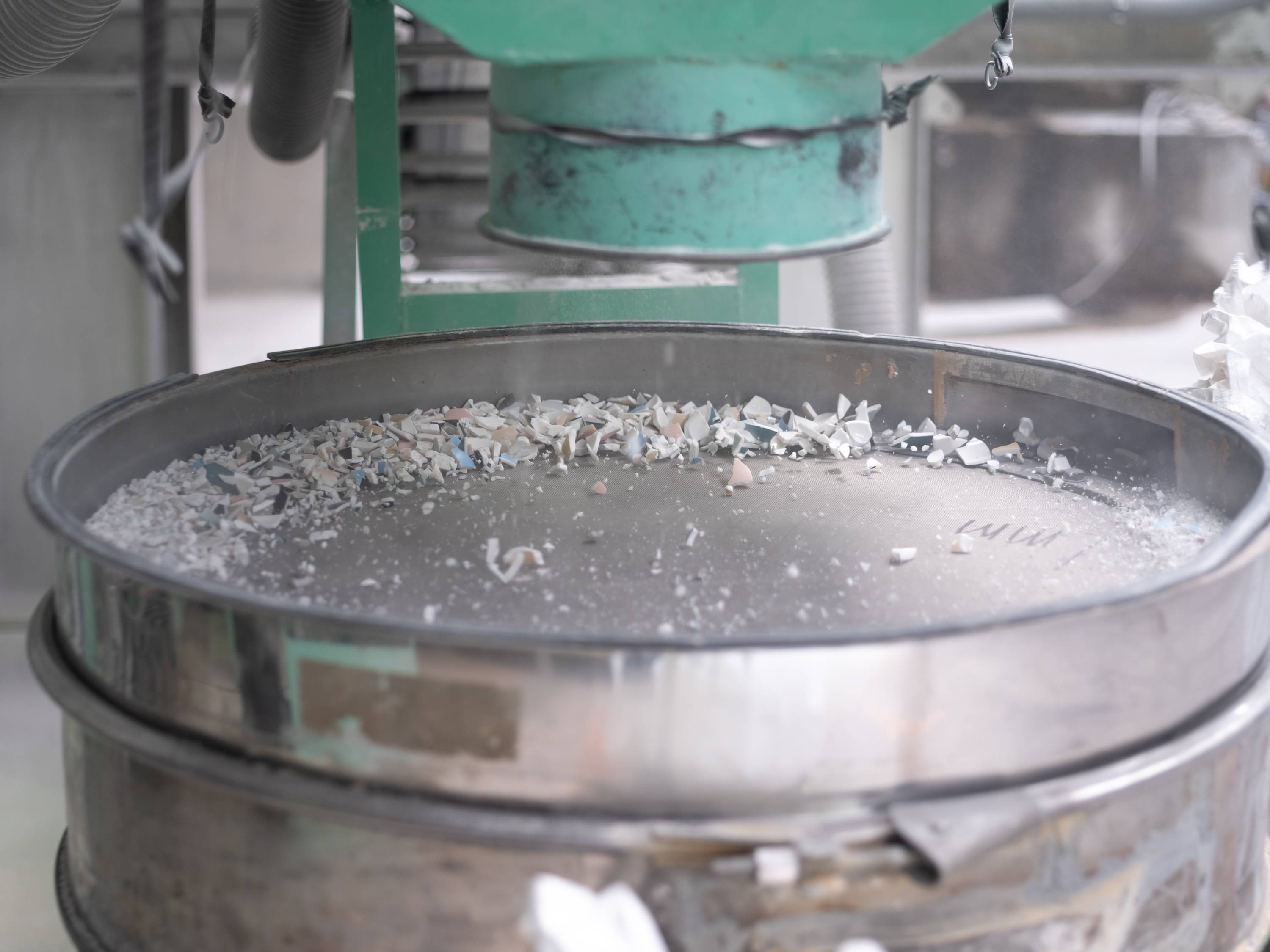
The fine fragments that remain after the third grinding process are removed by sieving. The content of recycled powder has a significant impact on the production of newly fired ceramics. It is important to perform the crushing and sieving processes precisely.
Process 4: Scene of kneading the powder into the soil
Ground ceramic powder

Recycled porcelain powder, which has been ground into small pieces during the grinding process, is mixed with pure porcelain clay.
ReWork's regulation is to use 20% of crushed recycled porcelain, and a large clay kneader is used to knead the clay while removing air firmly to produce a high quality clay.
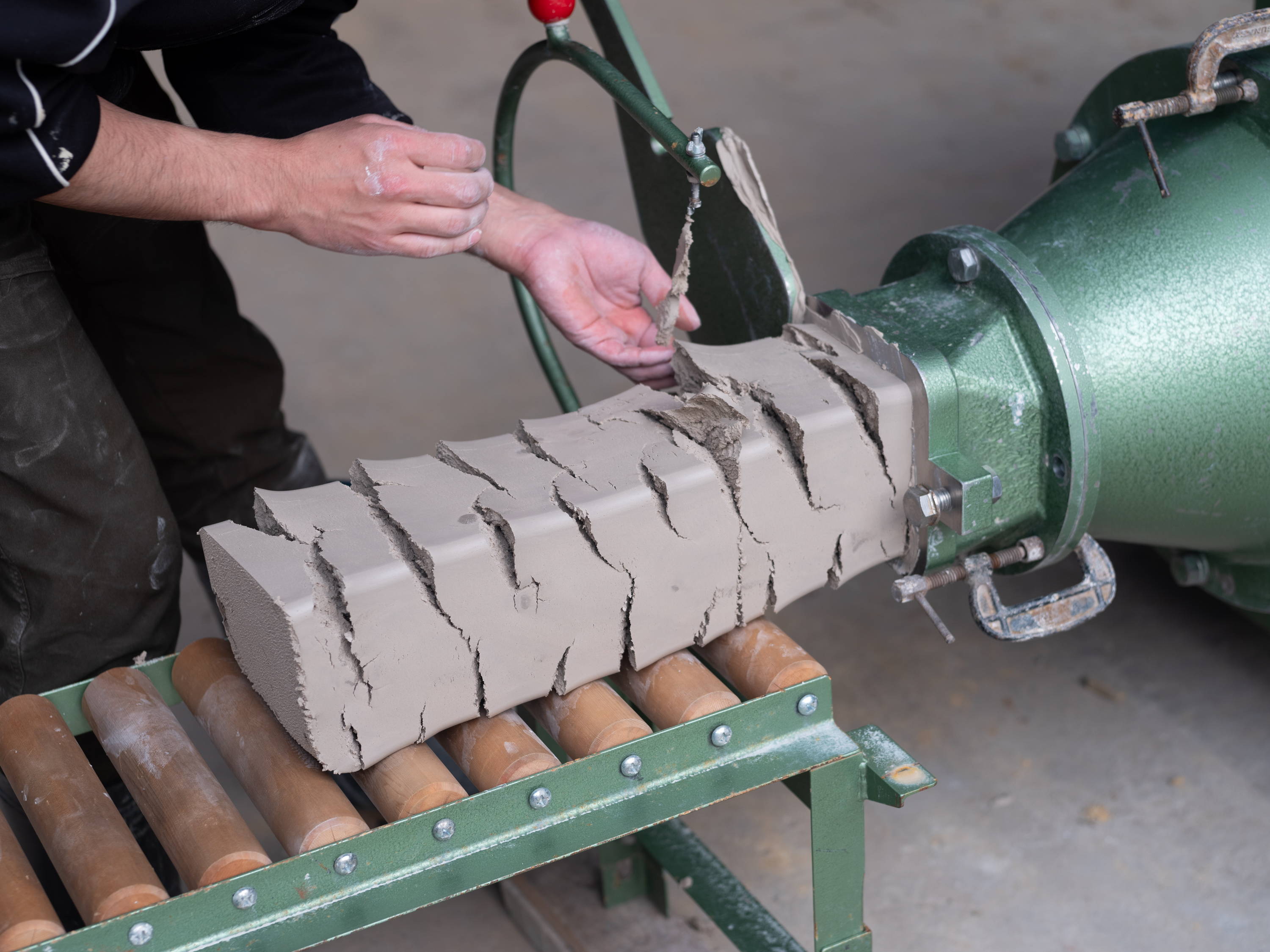
As with the crushing process, the clay is not completed once it is placed in the clay kneader.
The clay is kneaded repeatedly until the moisture contained in the clay and the crushed powder are well mixed.
Only when the clay is kneaded until it has a clean surface without cracks appearing on the surface can it be used as raw material as “recycled soil.
Process 5: Recycled soil dissolved in water is poured into a mold and molded to firing.
The raw soil is kneaded into a cylindrical shape and then dissolved in water at the appropriate volume to form a muddy solution called “mud plaster,” which is then poured into the mold for the product to be manufactured.
The molding of the ReWork Dripper is done by what is known in industry jargon as “pressure molding”. It is also how the existing ORIGAMI drippers are made.
In pressure molding, both the outer and inner molds are used, and when combined, they form a hollow plaster mold of the desired shape of the object.
As the name implies, the clay is formed by pouring muddy soil into a plaster mold under pressure using a special pump, which makes the soil particles denser and stronger.
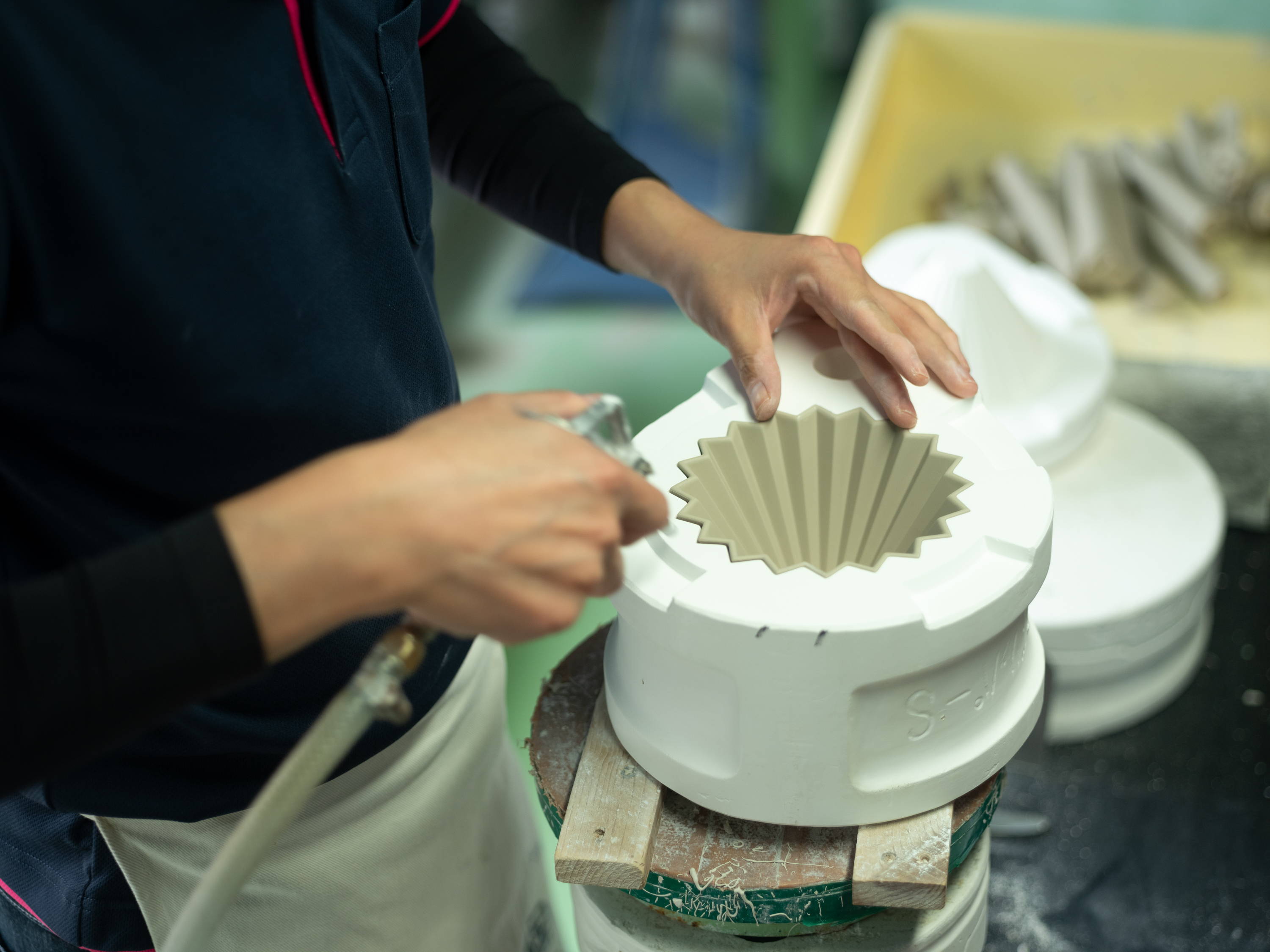
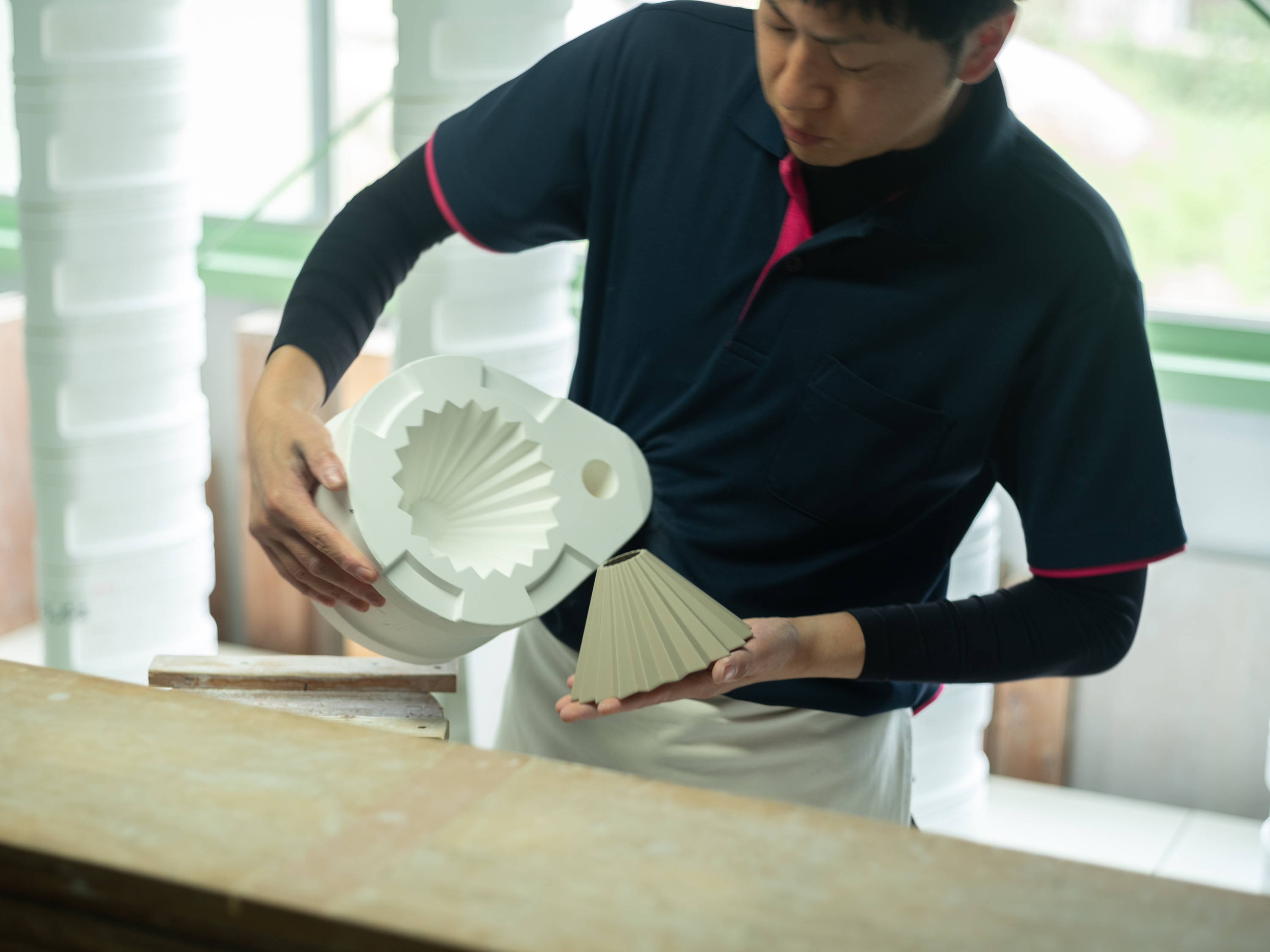
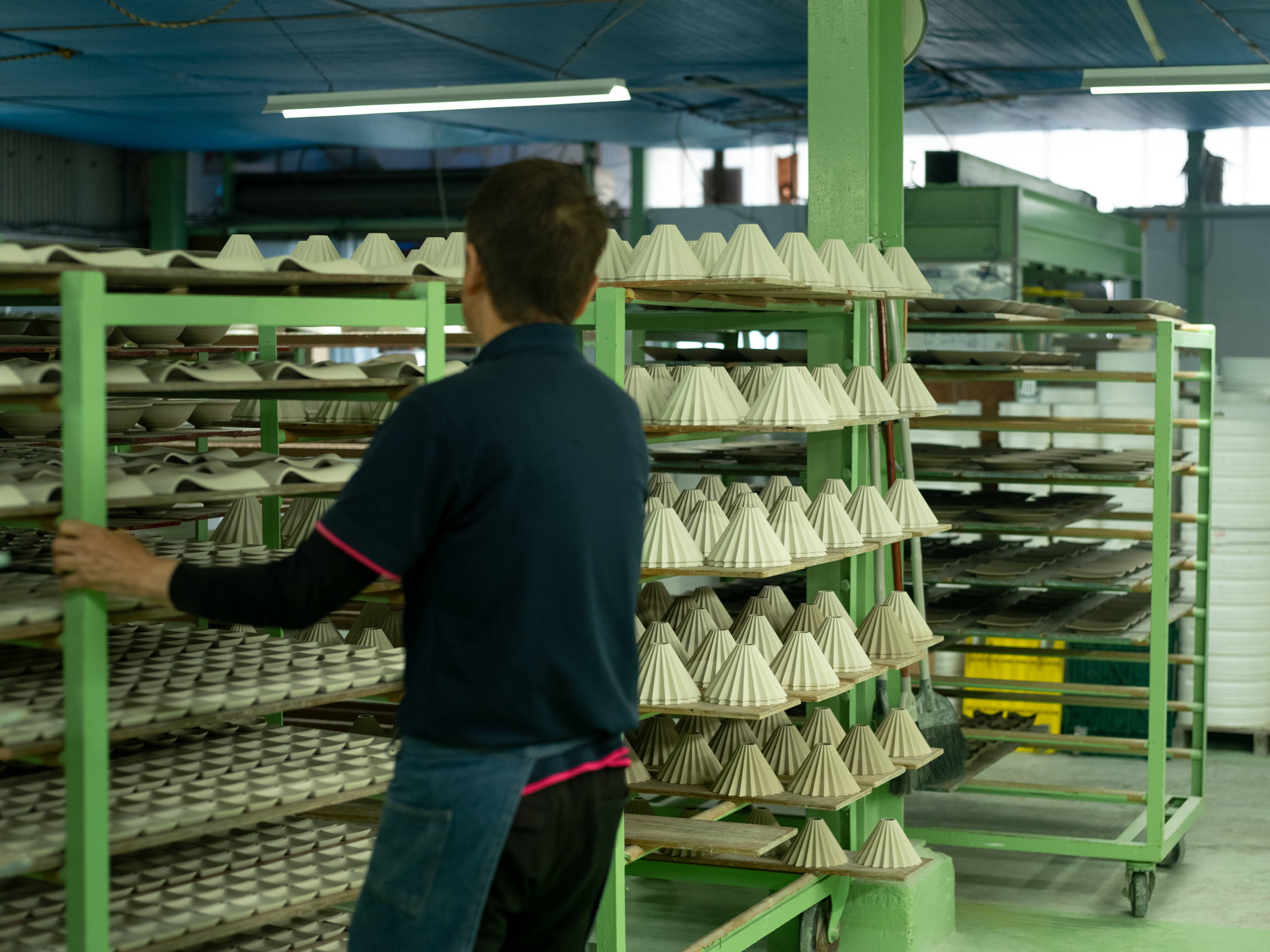
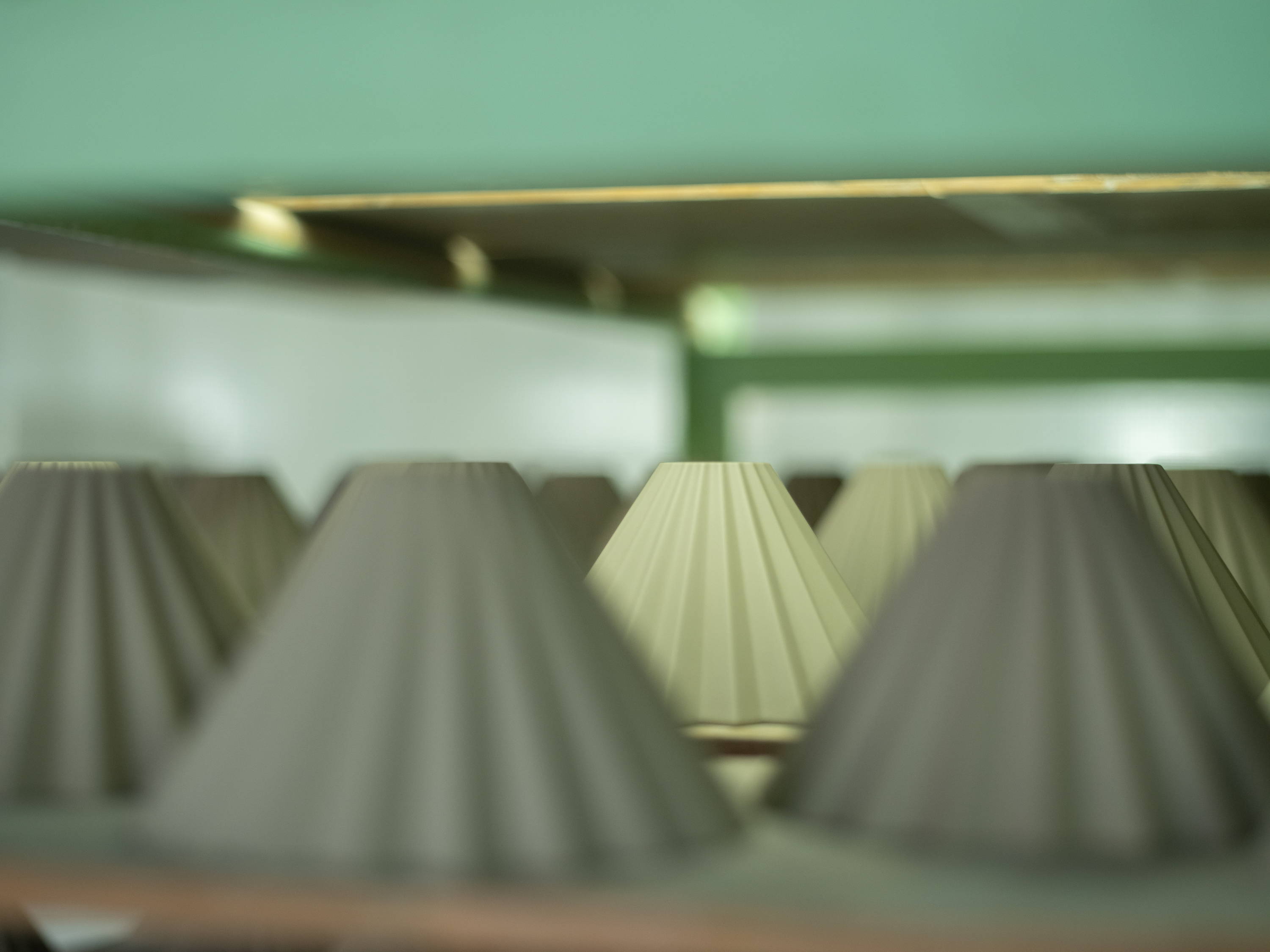
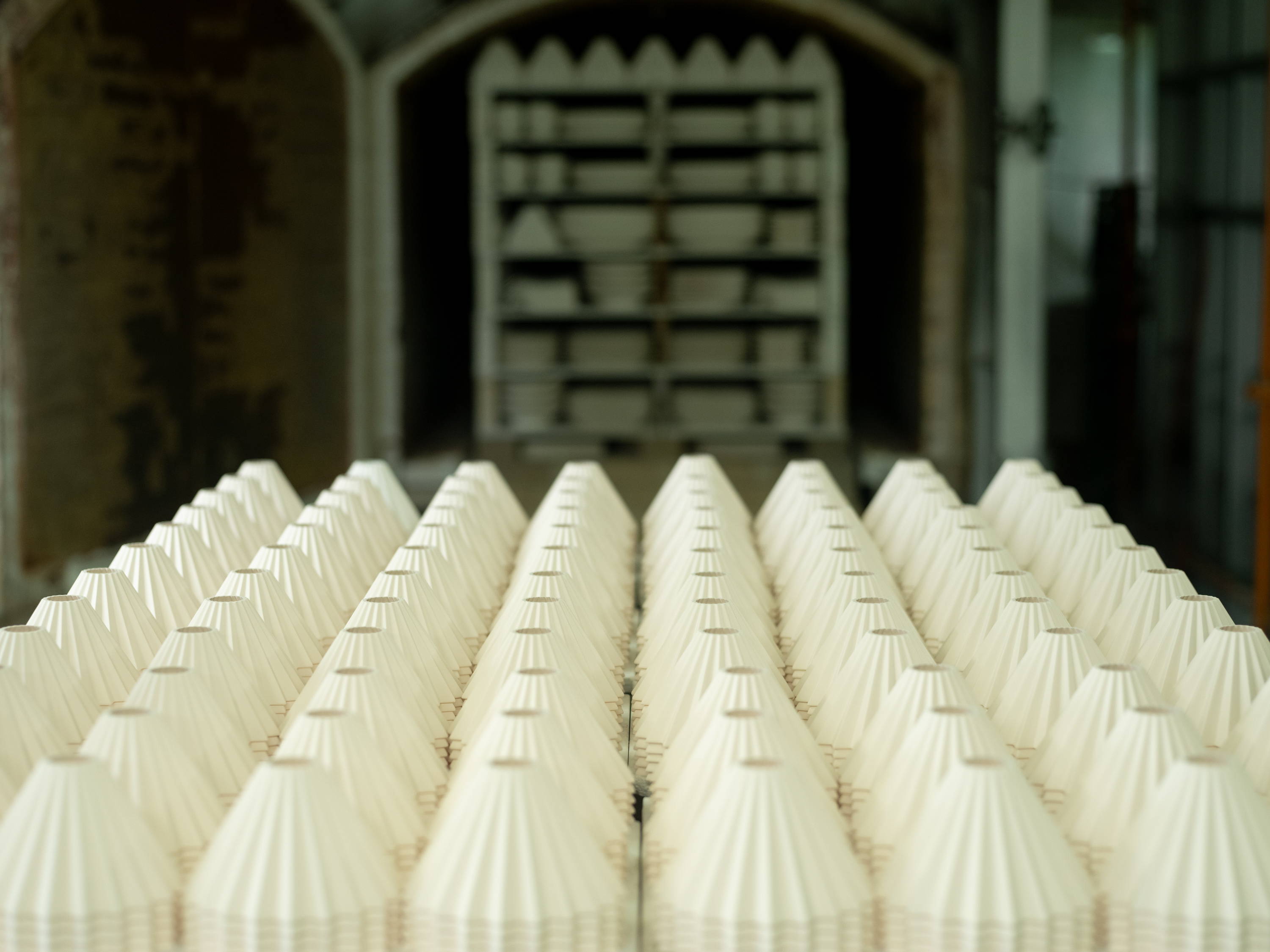
ORIGAMI's factory produces about 7,100 kinds of products per year,
including non-ORIGAMI products.
ORIGAMI alone produces 500 varieties of products per year.
The amount of ceramics and porcelain disposed of throughout the year is about 5-7% of the total production.
This is not only a problem for our company, but one that needs to be improved throughout Japan and the world,
First of all, we are aiming to establish an initiative to complete and recycle our own products.
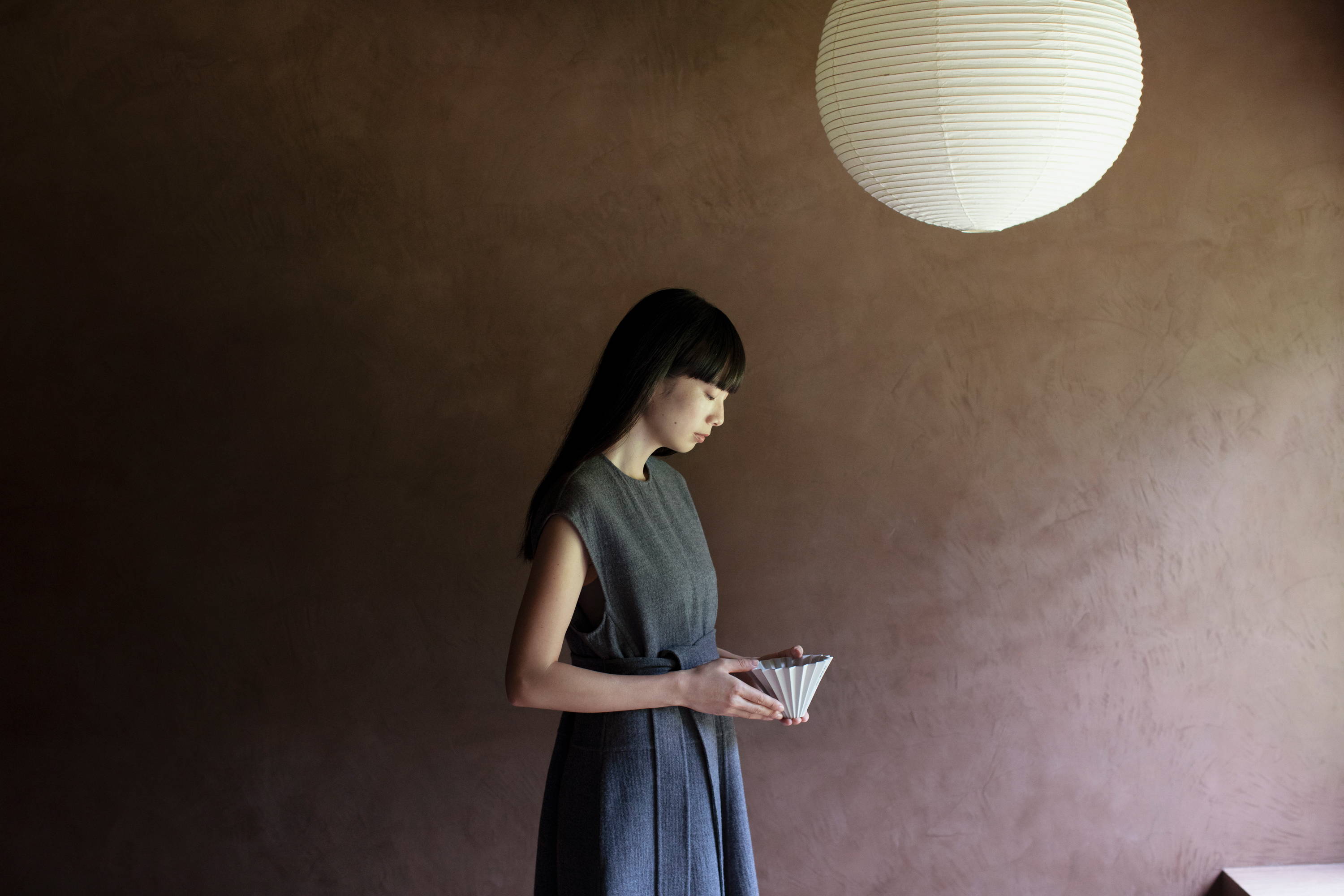
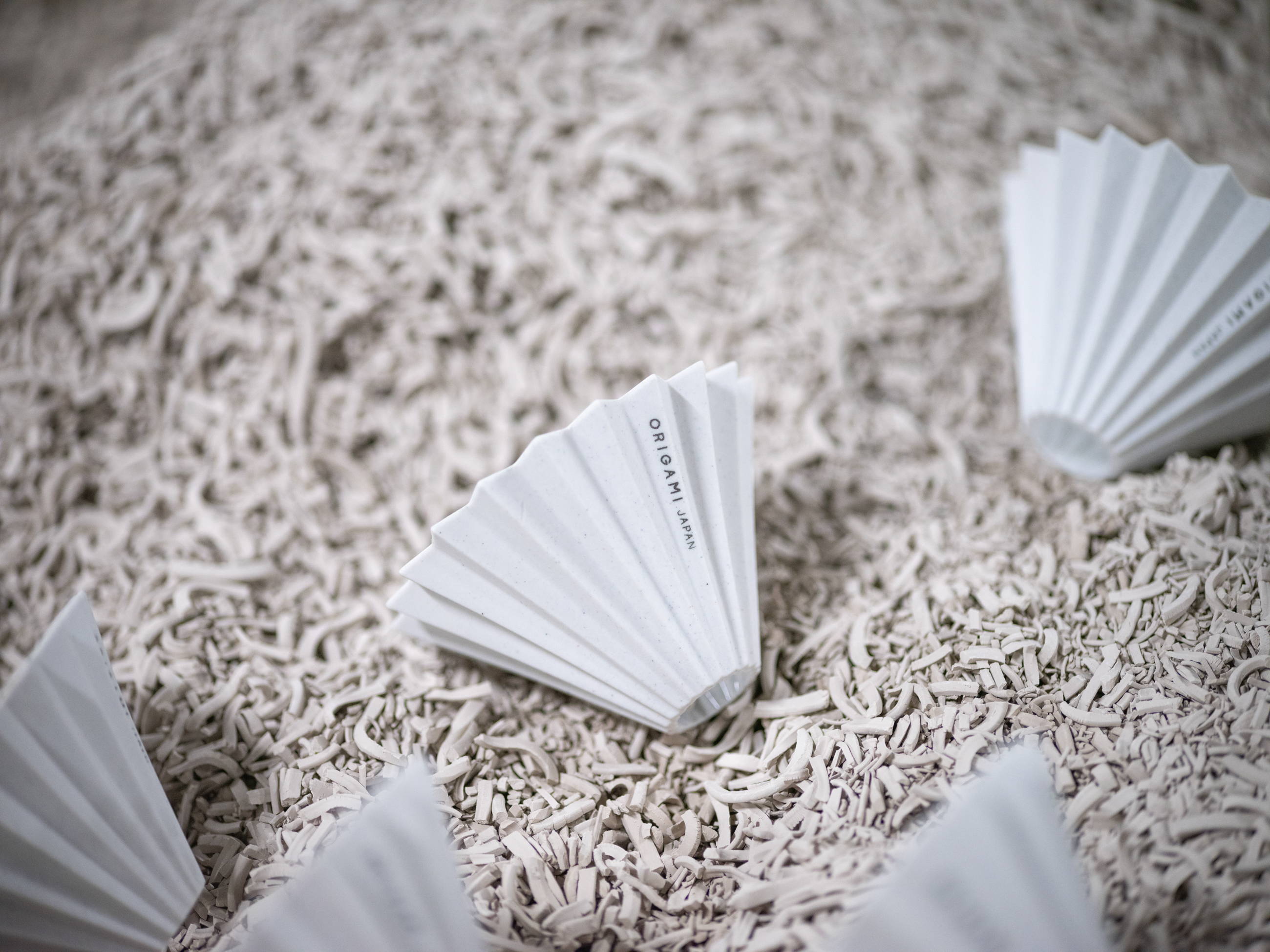

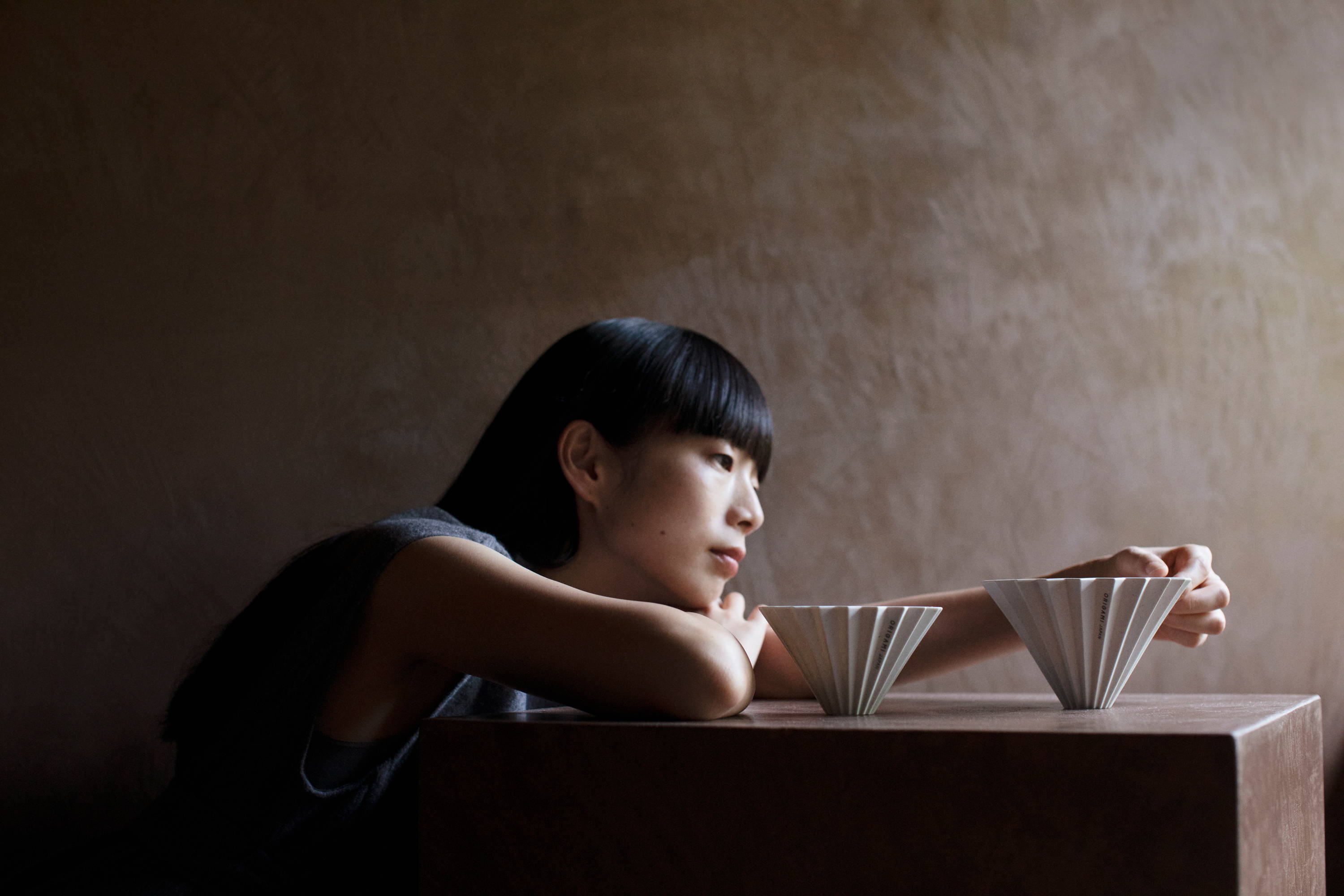
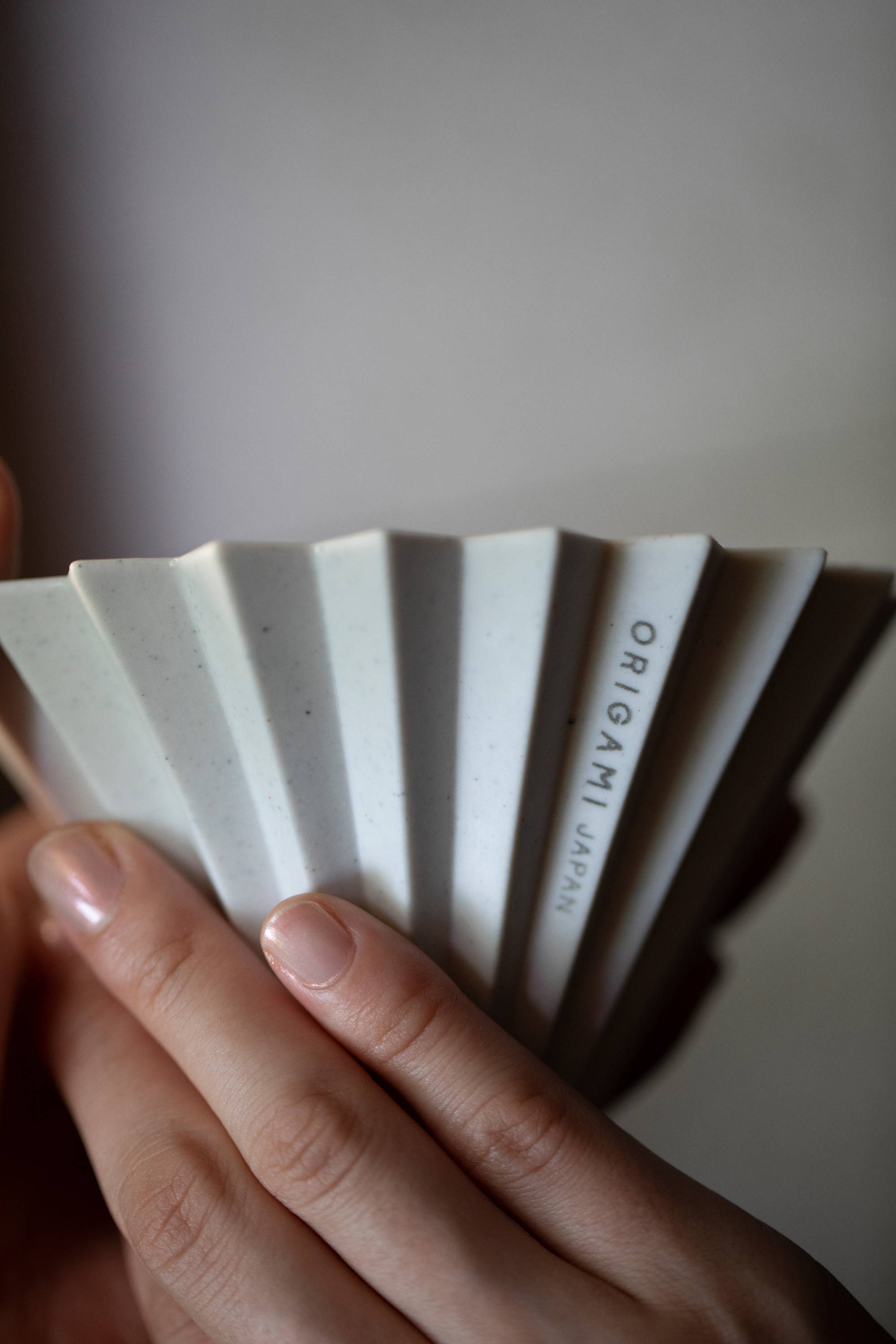
